“I am an old man now, and when I die and go to heaven there are two matters on which I hope for enlightenment. One is quantum electrodynamics, and the other is the turbulent motion of fluids. And about the former, I am rather optimistic.”
The above quote is often attributed to one of the greatest minds of the twentieth century, Werner Heisenberg. Although it may be of doubtful authenticity, the fact remains that turbulence troubled some of the greatest intellectuals of our civilisation, which include the likes of Aristotle, Leonardo Da Vinci and Ludwig Prandtl.
Richard Feynman described turbulence as “the most important unsolved problem of classical physics.”
The ubiquitous nature of turbulence manifests itself in several seemingly unrelated phenomena, from solar flares to rustling of leaves to the very familiar (and often scary) intense vibration of aircraft. Turbulence is an equally important subject in engineering as much it is in science, or perhaps even more. Almost all fluids motion around us is turbulent. However, our research in turbulence is still largely ad-hoc and the progress made, while incremental, restricts us from being wildly creative and efficient.
Our limited understanding of turbulence inhibits the progress of various technologies, such as aircraft and automobiles. And while a complete understanding of turbulence doesn’t look like something we’ll be able to get to in the near future, it is imperative that we use our limited knowledge of turbulence to our advantage.
Researchers around the world have been looking at ways to control turbulence and manipulate it in a manner that makes it more convenient for us. For instance, if we alter the flow right next to an aircraft’s surface, it’ll change the flow characteristics resulting in a change of drag experienced by an aircraft. In the grand scheme of things, this very practice might result in saving $150 billion of fuel every year.
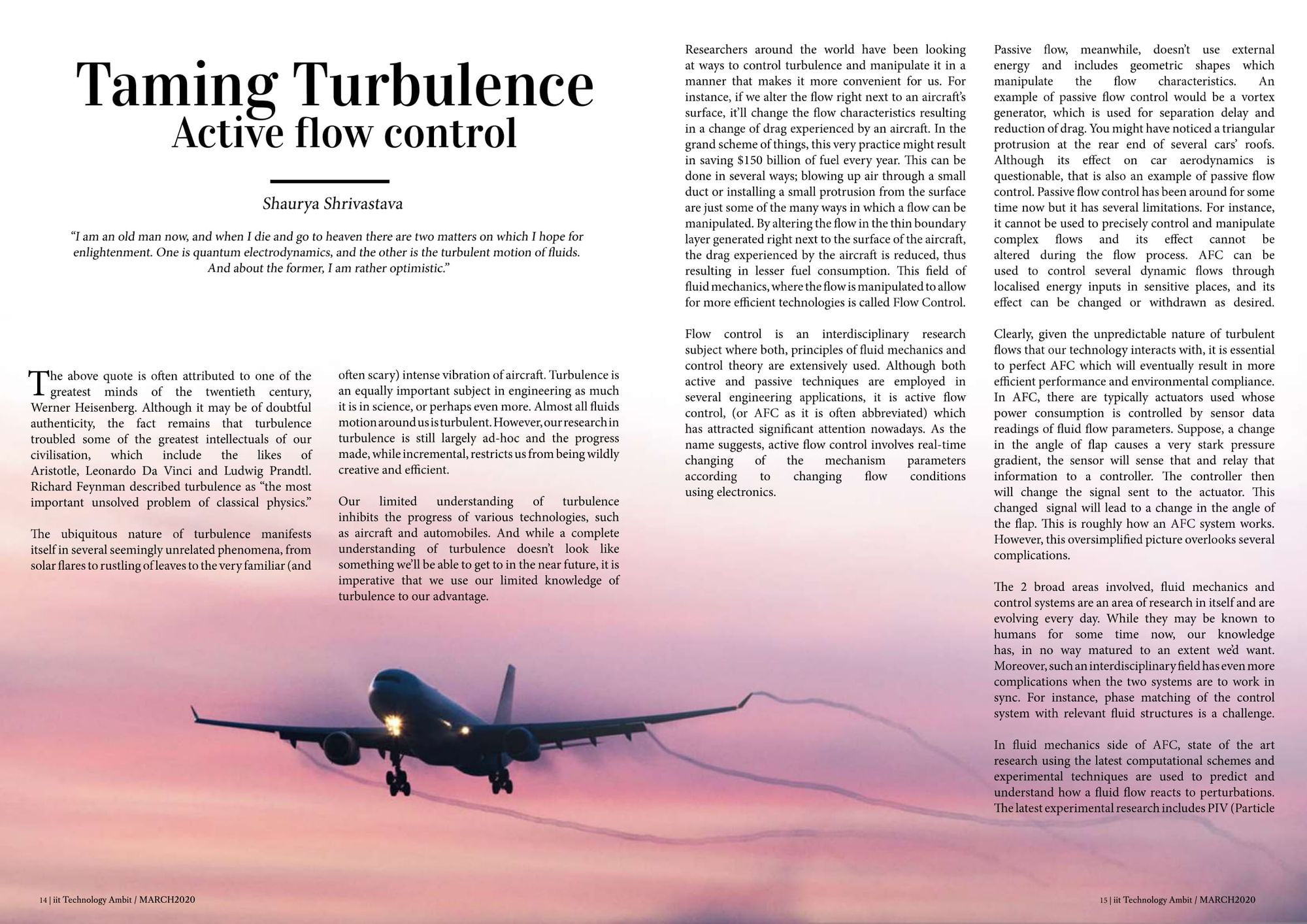
This can be done in several ways; blowing up air through a small duct or installing a small protrusion from the surface are just some of the many ways in which a flow can be manipulated. By altering the flow in the thin boundary layer generated right next to the surface of the aircraft, the drag experienced by the aircraft is reduced, thus resulting in lesser fuel consumption. This field of fluid mechanics, where the flow is manipulated to allow for more efficient technologies is called Flow Control.
Flow control is an interdisciplinary research subject where both, principles of fluid mechanics and control theory are extensively used. Although both active and passive techniques are employed in several engineering applications, it is active flow control, (or AFC as it is often abbreviated) which has attracted significant attention nowadays. As the name suggests, active flow control involves real-time changing of the mechanism parameters according to changing flow conditions using electronics.
Passive flow, meanwhile, doesn’t use external energy and includes geometric shapes which manipulate the flow characteristics. An example of passive flow control would be a vortex generator, which is used for separation delay and reduction of drag. You might have noticed a triangular protrusion at the rear end of several cars’ roofs. Although its effect on car aerodynamics is questionable, that is also an example of passive flow control.
Passive flow control has been around for some time now but it has several limitations. For instance, it cannot be used to precisely control and manipulate complex flows and its effect cannot be altered during the flow process. AFC can be used to control several dynamic flows through localised energy inputs in sensitive places, and its effect can be changed or withdrawn as desired.
Clearly, given the unpredictable nature of turbulent flows that our technology interacts with, it is essential to perfect AFC which will eventually result in more efficient performance and environmental compliance.
In AFC, there are typically actuators used whose power consumption is controlled by sensor data readings of fluid flow parameters. Suppose, a change in the angle of flap causes a very stark pressure gradient, the sensor will sense that and relay that information to a controller. The controller then will change the signal sent to the actuator. This changed signal will lead to a change in the angle of the flap. This is roughly how an AFC system works.
However, this oversimplified picture overlooks several complications. The 2 broad areas involved, fluid mechanics and control systems are an area of research in itself and are evolving every day. While they may be known to humans for some time now, our knowledge has, in no way matured to an extent we’d want. Moreover, such an interdisciplinary field has even more complications when the two systems are to work in sync. For instance, phase matching of the control system with relevant fluid structures is a challenge.
In fluid mechanics side of AFC, state of the art research using the latest computational schemes and experimental techniques are used to predict and understand how a fluid flow reacts to perturbations. The latest experimental research includes PIV (Particle Image Velocimetry) and other non-intrusive flow measurement techniques which are used to observe the flow behaviour and response to different categories of perturbations.
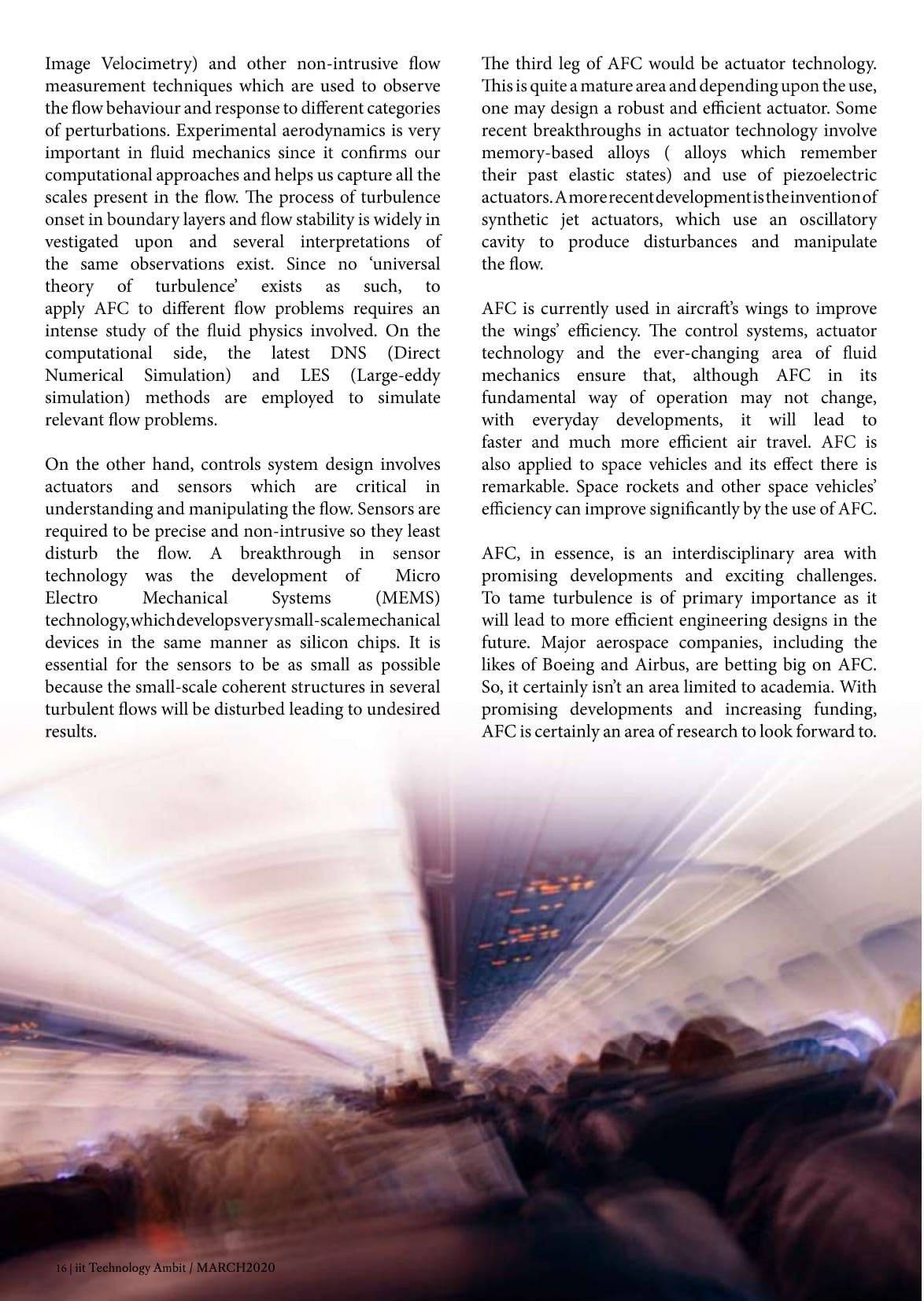
Experimental aerodynamics is very important in fluid mechanics since it confirms our computational approaches and helps us capture all the scales present in the flow. The process of turbulence onset in boundary layers and flow stability is widely investigated upon and several interpretations of the same observations exist. Since no ‘universal theory of turbulence’ exists as such, to apply AFC to different flow problems requires an intense study of the fluid physics involved. On the computational side, the latest DNS (Direct Numerical Simulation) and LES (Large-eddy simulation) methods are employed to simulate relevant flow problems.
On the other hand, controls system design involves actuators and sensors which are critical in understanding and manipulating the flow. Sensors are required to be precise and non-intrusive so they least disturb the flow. A breakthrough in sensor technology was the development of Micro Electro Mechanical Systems (MEMS) technology, which develops very small-scale mechanical devices in the same manner as silicon chips. It is essential for the sensors to be as small as possible because the small-scale coherent structures in several turbulent flows will be disturbed leading to undesired results.
The third leg of AFC would be actuator technology. This is quite a mature area and depending upon the use, one may design a robust and efficient actuator. Some recent breakthroughs in actuator technology involve memory-based alloys ( alloys which remember their past elastic states) and use of piezoelectric actuators. A more recent development is the invention of synthetic jet actuators, which use an oscillatory cavity to produce disturbances and manipulate the flow.
AFC is currently used in aircraft’s wings to improve the wings’ efficiency. The control systems, actuator technology and the ever-changing area of fluid mechanics ensure that, although AFC in its fundamental way of operation may not change, but with everyday developments, will lead to faster and much more efficient air travel. AFC is also applied to space vehicles and its effect there is remarkable. Space rockets and other space vehicles’ efficiency can improve significantly by the use of AFC.
AFC, in essence, is an interdisciplinary area with promising developments and exciting challenges. To tame turbulence is of primary importance as it will lead to more efficient engineering designs in the future. Major aerospace companies, including the likes of Boeing and Airbus, are betting big on AFC. So, it certainly isn’t an area limited to academia. With promising developments and increasing funding, AFC is certainly an area of research to look forward to.