"After four years, an engineering student might be able to tell you the stress and strain of a bolt, but may not know how to tighten it…" says an Axlr8r alumnus.
Started as a combustion team in 2006 by four motor enthusiasts, Axl8r Formula Racing, IITD was created to give students the chance to get hands-on practical experience and each year the Team is required to design and manufacture a new vehicle from scratch to be judged in the prestigious formula student competitions competing with teams from all over the world. So, while most engineering students might lack the practical applications of the knowledge they gained through books, a formula student stands out in this aspect.
Life of a Formula Student
"We run like an enterprise and hustle like a startup.” says an Axlr8r alumni, “Being a Formula student is like getting a peek into real-world engineering…The Axl8r club helps create industry-ready engineers. Formula Students are team players who have more practical knowledge than a lot of their peers, and having represented their institute at an international level, they also have a rare set of management skills and experience that gives them an upper hand when it comes to pursuing a core engineering field."
While Formula Students do have the exciting opportunity to represent their institute at an international level, there are many challenges that they have to face daily. "This is a great learning opportunity for the students, but the process requires much hard work and is a huge time commitment which might make it difficult for the student to give enough time to their academics. All team members shoulder a lot of responsibility and work in a high-pressure environment with dynamic situations. However, being part of the club, the students learn how to manage their time well and enhance their problem-solving skills and ability to stay calm in the face of a challenge." says a Senior Engineer at Axl8r.
Concerning their sponsors, the process involves the Team approaching different companies and pitching to them what the club has to offer. While most companies generally sponsor in-kind by providing them with the required material, rarely does any company provide monetary support. While the institute is trying to be supportive, the administrative processes, though necessary, are tedious and take up much time that the club cannot afford to spare. This is another major challenge for the club as money is the most limiting resource for creating a car.
Team Structure
The Axl8r Club has a multitude of departments. The current Team of 26 members is divided into the following departments, Chassis, Drivetrain, Brake, Suspension, Cooling, Accumulator, Safety, Electronic, and Wiring, BMS(Battery Management system), DAQ (Data Acquisition System), and Drive control which is the latest addition and is collectively working with the Suspension for Vehicle Modelling. While students from all years are welcome to learn, the first years generally gain knowledge of different fields by attending workshops and exploring their interests. The second-year students then take up the role of Junior engineers whose work is focused on their departments. Entering the third year, students become Senior Engineers who not only manage the second-year students but also get themselves familiar with other departments. The fourth-year students are Chief Engineers who are responsible for the smooth functioning of their departments as well as the overall functioning of the Team. And then, we have the Team Captain responsible for all the team members.
Getting better with each model
While they started with just one combustion vehicle, the current Team has just completed the club's fourth electric car for FS Italy next month, bringing the total number of cars in the institute to nine. Each vehicle has been made with changes and improvements, keeping certain points in mind. Talking about electric cars, a Senior Engineer says, "From 2016-2019, our goal for the vehicle had been to be able to clear all the technical inspections in FSG. Having done that, our focus was then shifted to the performance side as we tried to improve the dynamic performance of the car, which included increasing the overall voltage of our accumulator, having better motors that have a very high torque output, and overall decreasing the weight of the car, decreasing the assembly and disassembly time, the inclusion of sensors to measure different data and to increase the optimization and controllability of the car."
This was achieved by increasing the collimator voltage from 100 to 400 volts, putting in perfectly synchronous EMRAX 188 axial flux motors with peak torque of 90Nm, max RPM of 7000, and max power of 32kw, switching the Kelly inverter for CAN communicable PM100DZ propulsion inverter, adding Self-developed battery management system for SOC (State of Charge) estimation and replacing Simple planetary gearbox for Compact and light step planetary gearbox assembly, the only Indian Team to have done that yet, which led to 35% reduction in weight and 45% reduction in volume. The Air cooling was switched to a more efficient Water cooling of the inverter and motor. While the previous model only had the compulsory sensors (i.e., Throttle potentiometer, Thermistor, pressure sensor), we observe a Sensor integration of many more sensors in the new model, which enables data acquisition (steering sensor, potentiometer at damper, IMU, IR sensor, Pressure and temperature sensor in brakes and cooling line). This data is stored in an installed SD card.
The main disappointment for the Team was their inability to procure a monocoque chassis due to their budget limit. After making such changes in its gear, the Team had to design the vehicle now to fit all these newly acquired improved goods into a compact model, which was a challenge.
Overcoming Covid-19
While Covid-19 disrupted all our lives, the timeline with which the club had been working since its beginning, which included designing the car in august-December, manufacturing in the months of Jan-April, and testing in the months of May-June, and then finally competing in FSG in August, was highly disturbed. But the Team soldiered through, focusing mostly on the designing aspects in the online mode and starting the manufacturing as soon as the campus reopened. The current Team also had to overcome the lack of practical and technical skills that they had been unable to acquire due to the online semester. So when the campus was opened, the new team members, especially the ones that had just been promoted to senior roles, had to learn those skills in a short span of time while also being responsible for their juniors and helping them get a handle on things.
What does the Future Hold for the Team
When enquired about their future goals and upcoming competitions, a Senior Engineer said, "Getting back to our original timeline is crucial to keep the members motivated, and then, we would like to catch up with current technological advancements and start laying down the groundwork to go driverless." To achieve the goal of creating a driverless vehicle, the Team is currently working on a DC-DC converter (400 volts-24 volts), which will soon be completed. Other than that, they are working on Live Telemetry through 4G LTE Module, implementation of control Algorithm, Cell modelling and Simulation of motor and inverter, and refinement and testing of their self-made vehicle model to make the vehicles realistic.
Creating History
Since its formation, the Team has participated in numerous competitions on both national and international levels, and in 2019, the Team's hard work paid off as they became the first Indian electric Team to clear all technical inspections in Formula Student Germany (FSG). Not only that, but they also performed exceedingly well at the virtually held Formula SAE Australasia 2020, becoming India's first electric Team to have won two international podiums in a single competition by achieving the first position 'Cost Event,' which included a BOM (bill of material) that included all parts of the car including the smallest of nuts and screws with the explanation of how one would manufacture it in detail and second position in the 'Business Event' which includes developing a business model around the car and pitching it to the judges much like as we see in the show 'Shark Tank .' They also ended up performing incredibly well in Formula Bharat 2021, winning the first position in the Business event, the third position in the Engineering Design event, Best Powertrain Design Award, Innovative Concept Award in the Business event, Best Financials Award in the Business event and an overall second position in the competition itself.
Although the team has achieved various accolades, it is yet to win the title of the best Indian team. They may have faced challenges but then again, so have other Indian teams. A larger question remains unanswered,” What does an IITian team lack?” Even though the team may have resources and talent, talented freshers prefer joining other teams and clubs in the institute instead of risking it all to work in an FS Team; why?
A bigger question remains: " India may have been a hub to an ever-blooming IT sector; why could it not provide the same environment for innovation and product designing?” Perhaps we could find answers to our questions by looking into the ratio of learning and development that a team member receives to the invested effort. A difference in this ratio is a significant decision-making factor that this generation takes seriously. It would not hurt to presume that the learning to risk exposure ratio is also pivotal in decision making.
The Axl8r Team seems to have had a good run in this pandemic, and while things might not have been easy, they have proved that if you put in the hours, you reap the benefits. Let’s hope that they keep up this streak and keep on making IITD proud.
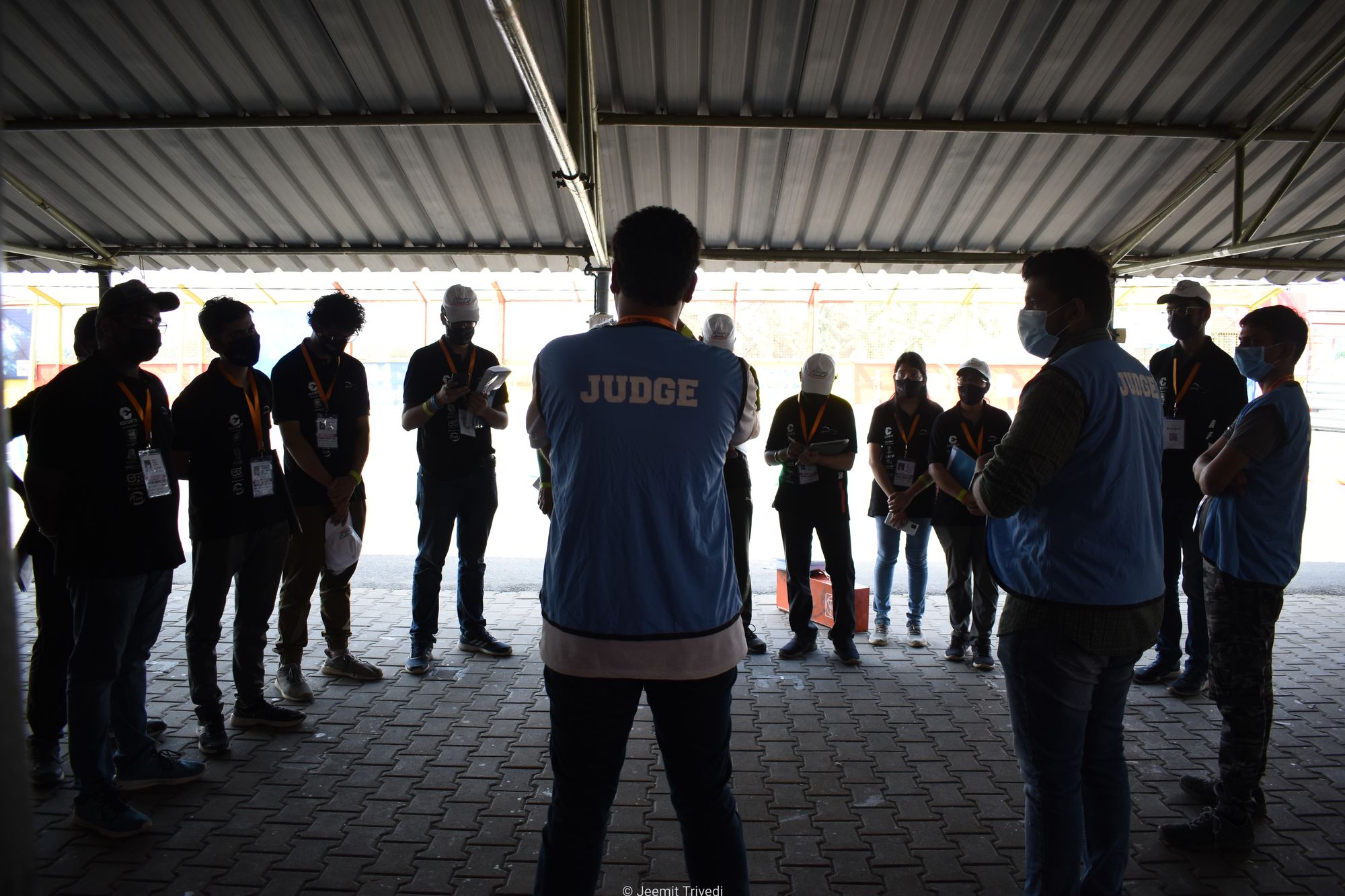
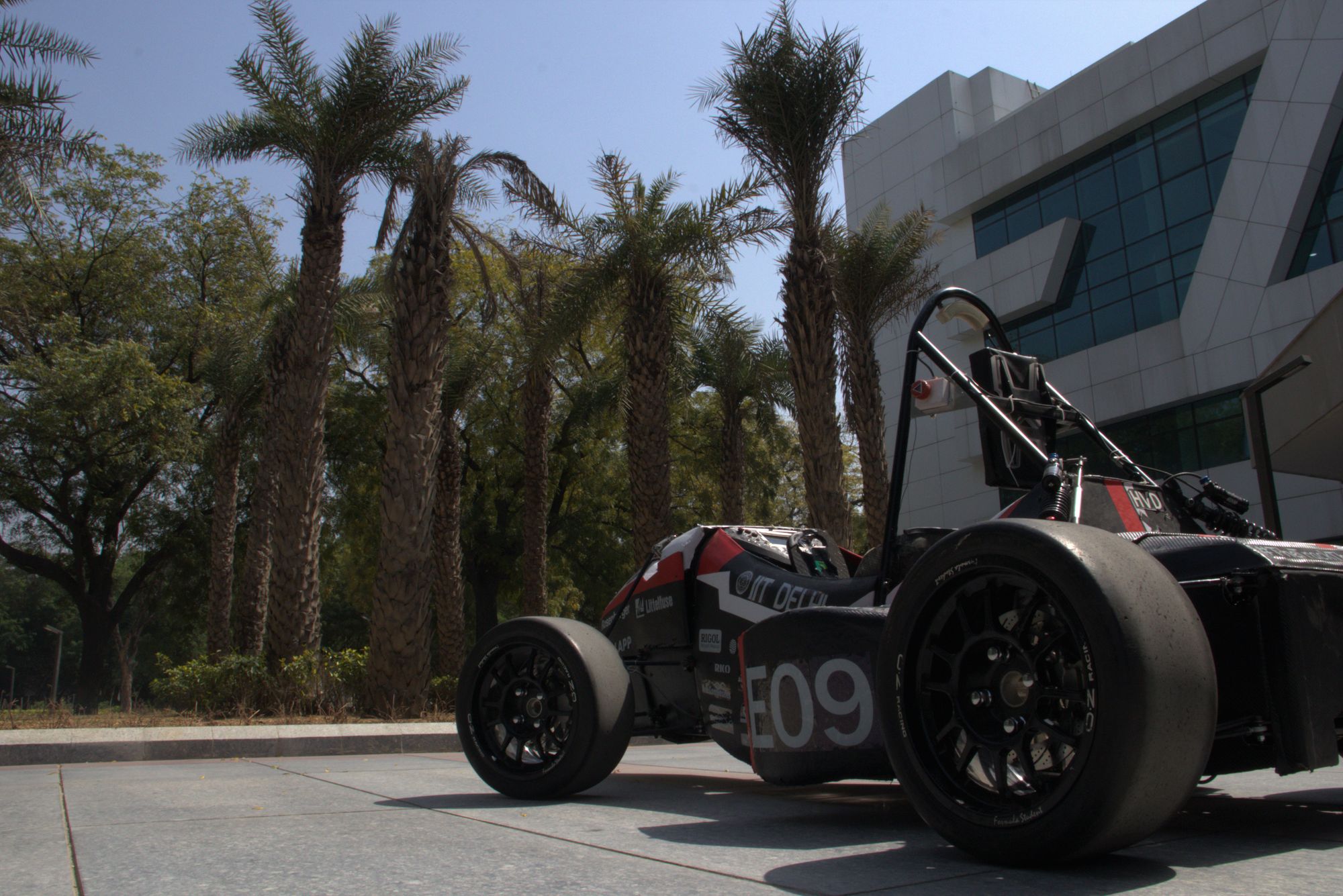
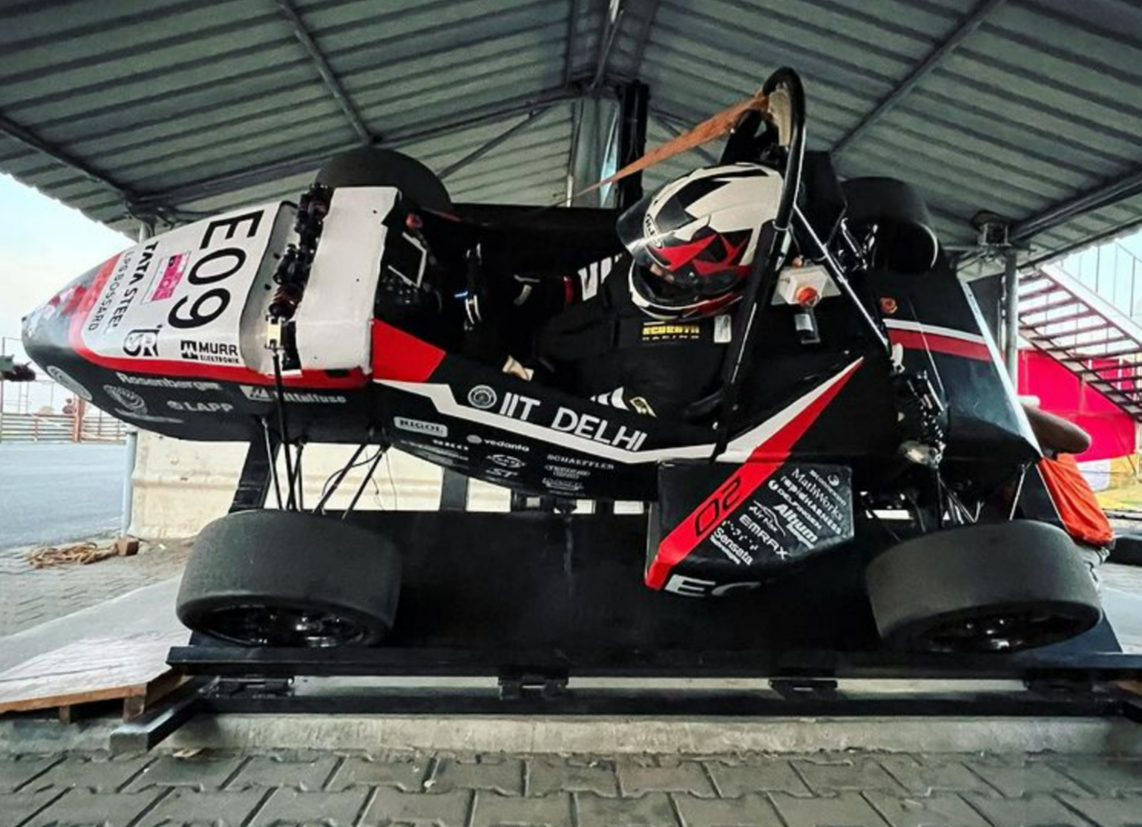