It is clearer now more than ever that the agricultural industry of India is the backbone of the country. Although it carries immense potential, it has often been neglected in the past. With poor agricultural practices, exploitation, unpredictable climate change and limited initiatives in research and development to improve the condition of this sector, farmers have long been the brunt bearers of these issues. Expecting governmental measures to deal with these affairs is a valid demand but is a passive and slow process when in fact these matters need immediate attention. Driving innovation in agriculture based technology is among the most promising ways of overcoming the fix that we seem to be in.
IIT Guwahati sets precedent in the matter by organising a unique competitive event in Inter IIT Tech Meet 9.0 known as the Agrobot Design and Innovation Challenge. As the name suggests, the competition required participating teams to develop models for agricultural bots addressing one or more of the four major problems identified from the perspective of a farmer.
A team from IIT Kharagpur managed to bag the first position in this event. The team of nine students, namely - Adarsh Goyal (Captain), C Siva Vignesh Krishnan, Saumitra Joshi, Dhananjay Sunil Kulkarni, Azad Jitendra Jagtap, Shreyans Ray, Shrey Verma, Divyanth LG, Anirudh Gupta, was led by two professors - Prof. Aditya Bandhopadhyay from the Mechanical Department and Prof. Peeyush Soni from the department of Agriculture and Food Engineering. The assembled members tried their hands at an extremely ambitious approach of addressing as many problems as they can, out of the four given, in a very limited amount of time and came up with an incredible solution that makes one wonder how much progress we could make if we truly tapped into the potential of such bright young minds.
PROBLEMS CHOSEN
The team decided to address three of the four problem statements -
- Mechanised farming in hilly terrain
- Seed metering mechanism for uneven or irregular seeds
- Transplantation
These problems, although had been handled individually in the past, had never been addressed in a single automated bot which brings about the commendable novelty of this project. Such an endeavour came with various challenges and prospects -
- Building a bot for a hilly terrain is a completely different ball game that comes along with a lot more obstacles than that of a plain terrain. One now needs to tackle additional complications with regards to maneuvering, alignment with steep edges, plowing, seeding, and so on.
- The process of sowing is also very intensive, requiring a lot of time, effort and precision since various aspects like metering, soil penetration, and the correct amount of seed to drop in the right location have to be taken into consideration. Automating this process would not only reduce the intense manpower required but also fasten the affair along with improved precision for a better laid out farmland.
- Losing out on crop space when implanted seeds don’t grow is an issue which can be tackled with transplantation. It allows us to maximise the crop grown on a piece of land. However, it is a tough procedure to be automated since it needs to be handled tenderly considering the fragile nature of samplings.
SOLUTION - KRISHI-VARDHAK
The team came up with an ingenious modular approach to address all these issues in a single agricultural bot which they named ‘Krishi-Vardhak’.
- Seed metering mechanism: When seeds are added into the container of the bot, they begin to fall into a detachable metering plate with cups that hold the seeds individually. The rotations per second (RPM) of this metering plate are synchronised with the motion of the bot such that seeds fall at regular intervals. The RPM of the plate can be changed as per any specific requirements. Since the plate is detachable, the mechanism can cater to many kinds of crops which varying seed types by replacing it with the corresponding plate with cups meant to hold that particular seed efficiently.
- Transplantation mechanism: the saplings are placed on gravity rollers so that they can easily be pushed by a spring supported plate to fall down on a tray with a rotating flap. The RPM of the flap is also synchronous with the motion of the bot to ensure proper distancing between saplings before they fall through a tube on the land. The primary feature of this arrangement is that the angle of inclination of the tray can be changed as per the slope of the hill.
- Weeding mechanism: Although this wasn’t picked as a problem that the team aimed to handle autonomously, the traditional method used by previously developed technology for weed removal was also implemented as part of their model.
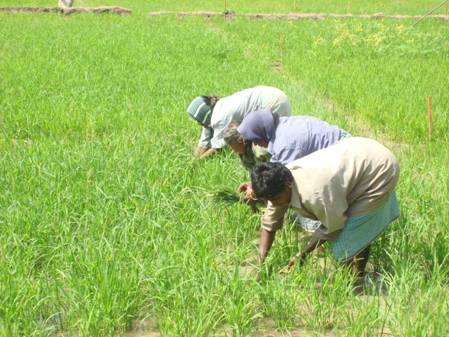
Advantages of this technology:
- Modularity: The modularity of the product is what sets it apart. Whichever function one needs to perform i.e. seed metering, transplantation or weeding, the basic machinery remains constant, only the relevant modules have to be attached to achieve the task. This reduces costs and the power required for operation.
- Universality: the team tried its level best to make this technology applicable for all kinds of crops and terrains by providing options like changing the metering plate as per the kind of seed of the crop, changing the RPM of the metering plate or the flap, and changing the inclination of the transplantation tray.
- Practically realisable: The product has especially been designed while considering the feasibility of bringing it into the market. It is extremely cost effective and uses materials easily available in the market, e.g. aluminium extrusions for the chassis. The components are also easy to manufacture. Above all, the bot has varied applications that it can serve single handedly.
It needs to be acknowledged that it was no small feat that this team of students managed to achieve especially in the little amount of time they had. This shines light on how important it is to involve bright minds like these in agricultural innovation, since it could prove to be the most promising path to an agricultural revolution!
Special thanks to Adarsh Goyal for taking out the time to explain their product to the author to help write this article.